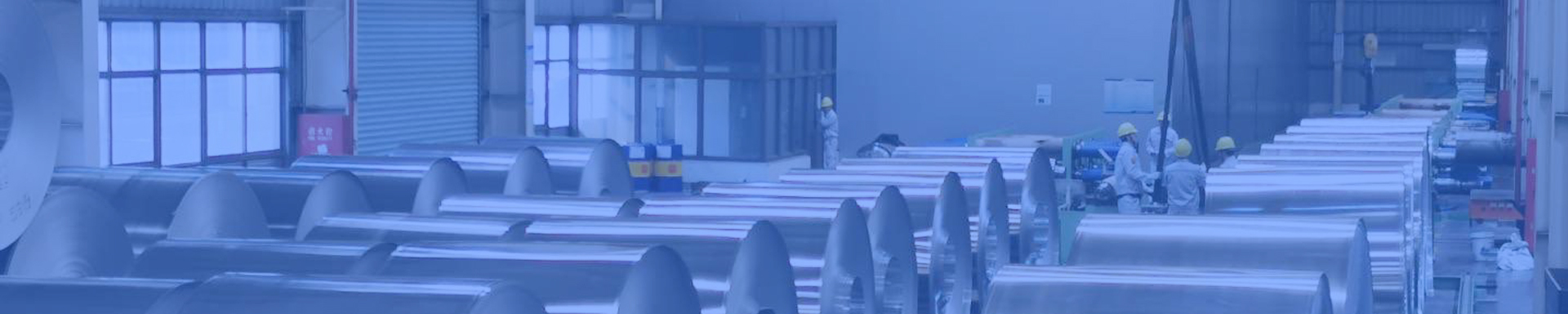
Hot Rolling Mill Machine Of Operate Side Work Roller Rolling Mill Block Shaft
Our company has DMG DMF1800*600 five-axis machining center, horizontal machining center,vertical machining center,gantry machining center and high-precision three-coordinate inspection.
Work Roller Rolling Mill shaft block is one of GW precision key products.
- GW Precision
- China,Luoyang
- Contractual Stipulation
- Anual Capacity of Steel Spool is 4000 pieces
- Information
Hot Rolling Mill Machine Of Operate Side Work Roller Rolling Mill Shaft Block
(Suitable for hot rolling production lines of plate and strip/section steel)
1、 Application scenarios
1. Core functions
Roller positioning and force transmission:
Maintain the stability of the working roll under the action of rolling force (maximum 30MN) and bending force (± 1000kN)
Endure the instantaneous impact load of biting steel (impact coefficient 2.0-3.5)
Thermal management:
Working in a rolling temperature environment of 400-800 ℃, the instantaneous surface temperature can reach 300-450 ℃
Need to resist periodic thermal stress (>10 ⁵ cycles/year)
2. Typical working conditions of mill shaft block
Mechanical load: Hertz contact stress 1000-1500MPa, torsional vibration load (critical speed should avoid working speed 1.5-2.5 times)
Wear environment: Iron oxide scale abrasive particles (HV800-1100)+rolling lubricant high-temperature carbonization deposition
Material selection and optimization of the Work Roller Rolling Mill shaft block
1. Base material
Material grade, core advantages, applicable scenarios
50CrMoV high temperature strength (σ 0.2 ≥ 650MPa at 500 ℃) wide and thick plate rolling mill (roll body>3m)
Low cycle fatigue performance (Nf ≥ 5000 times at Δ ε t=1%) of 38CrNiMoV high-strength strip steel during rolling
H13 improved heat-resistant cracking (thermal conductivity 24W/m · K) stainless steel hot-rolled
2. Key reinforcement technologies
Bearing mating surface:
Laser quenching (hardening layer depth 2-3mm, HRC54-58)
Plasma spraying WC-10Co4Cr (porosity<0.8%)
Threaded connection area: boronizing treatment (Fe2B layer 50-80 μ m)
3. Innovative material applications
Gradient functional axis:
Core: 25Cr2MoV (high toughness)
Surface: Stellite 21 (resistant to high temperature wear)
Diffusion bonding through hot isostatic pressing (HIP)
3. Heat treatment system
Vacuum quenching: 1020 ℃ × 3h (nitrogen cooling)
Double tempering: 560 ℃× 4h+520 ℃× 6h (oil cooled)
Stabilization treatment: Deep cooling (-120 ℃× 8h)+aging (250 ℃× 24h)
4. Surface strengthening
Composite processing:
Shot peening (Almen strength 0.4-0.45mmN)
Ionic sulfurization (FeS layer 1-2 μ m)
Laser texturing (Sa=3-5 μ m)
*Key processes:
Constant temperature grinding of bearing position (coolant 20 ± 1 ℃)
Electrochemical machining of transition fillet (R angle accuracy ± 0.05mm)*
Typical parameters of Work Roller Rolling Mill shaft block
Requirements for parameter indicators
Axis diameter tolerance of φ 320 ± 0.008mm
High temperature creep rate ≤ 1 × 10 ⁻⁷%/h (500 ℃/200MPa)
Vibration acceleration ≤ 4.5m/s ² (ISO 10816-8)
The service life of this shaft in a hot rolling mill is 2-3 years (with an annual rolling capacity of 1.5-2 million tons), and it can be extended to 5 years using gradient materials. The proportion of thermal fatigue failure is greater than 60%, and the current research and development focus is on nanostructured thermal barrier coatings.