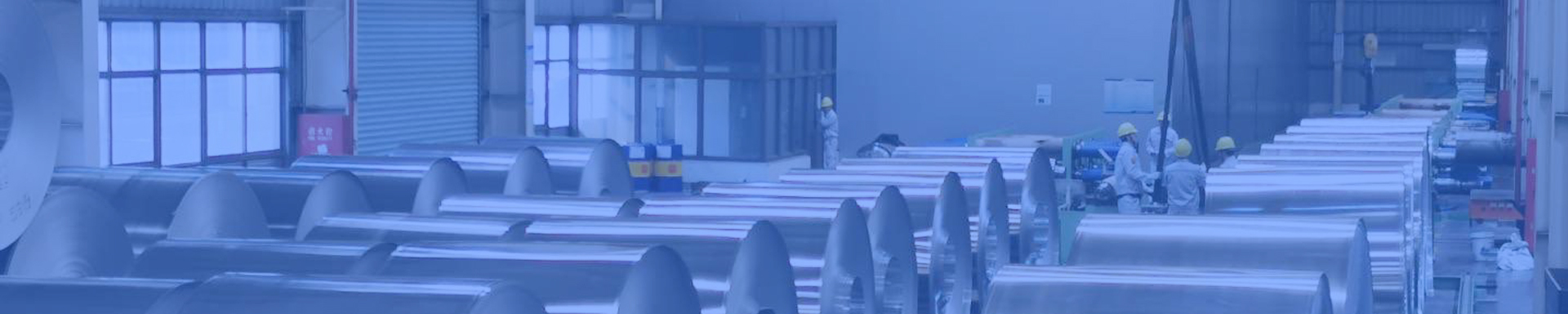
Bearing seat for transfer side working roll of hot rolling mill
The bearing seat of the working roll is one of key products of GW precision.
List Core functions and operating requirements of the bearing seat of the working roll on the transmission side of the hot rolling mill as the following:
Core functions
Torque transmission: responsible for the torque transmission from the main transmission system to the work roll (peak torque can reach 500kN · m)
Dynamic load support: capable of withstanding rolling force (2000-6000kN on one side) and alternating impact load
Accuracy maintenance: Ensure that the radial runout of the work roll is ≤ 0.04mm (guaranteeing a thickness tolerance of ± 0.15% for the strip steel)
Adapt to working conditions
Temperature range: Bearing position working temperature 80-120 ℃ (instantaneous peak 180 ℃)
Rolling speed: ≤ 15m/s (up to 20m/s when paired with oil film bearings)
Roller replacement frequency: ≥ 1 time/shift (requiring quick disassembly and design)
- GW Precision
- China,Luoyang
- Contractual Stipulation
- Anual Capacity is 500 pieces
- Information
Bearing seat for transfer side working roll of hot rolling mill
Material and manufacturing standards for the bearing seat of the working roll on the transmission side of the hot rolling mill
Main material
Brand: ZG35CrNiMoV (special grade cast steel)
Ingredient optimization:
|Elements | C 0.33-0.37 | Cr 1.0-1.3 | Ni 1.2-1.6 | Mo 0.3-0.5 | V 0.15-0.25|
Performance advantages:
High temperature strength (σ ₀. ₂ ≥ 650MPa at 300 ℃)
Fatigue life (Nf ≥ 2 × 10 ⁶ times at Δσ=400MPa)
Key component materials
Surface hardness of component materials after heat treatment
Bearing seat of the work roll body ZG35CrNiMoV quenched and tempered+aged HB 300-330
Torque transmission keyway 42CrMoA nitriding treatment HV 800-900
Sealed end cap duplex stainless steel 2205 solution treated HRC 28-32
Heat treatment and surface treatment of the bearing seat of the working roll on the transmission side of the hot rolling mill
Heat treatment process
A [Electric arc furnace melting] -->B [Argon protection pouring]
B -->C [880 ℃ × 6h normalizing]
C -->D [850 ℃ oil quenching+620 ℃ tempering]
D -->E [-80 ℃ × 4h cryogenic treatment]
surface strengthening
Bearing hole hypersonic flame spraying (HVOF) WC-12Co coating (thickness 150-200 μ m, HV ≥ 1300)
Laser quenching of sealing surface (hardening layer depth 1.2-1.5mm, HRC ≥ 52)
1、 Vertical Machining Center: According to the view shape milling depth 5mm to find the positive belt (each side has room for 1.5-2mm); clean and remove burr sharp edge for inspection. (first piece for inspection)
2、 Horizontal boring machine :It is found that a margin of 1.5 -2 mm is reserved for each surface of the normal belt, and the margin of the groove in the view is 1.5-2 mm; the margin of the hole in the hole is 3-4 mm; the length of each hole is 2-3mm; and the clear edge is used for removing the sharp edge of the burr for inspection. (first piece for inspection)
3、 Vertical Machining Center: Finish milling to (non-tolerance fit surface) requirements, milling length to find the right edge depth of 5 mm; boring to the requirements, each side of the residual amount of 1 ≤ 1.5 mm; each hole length to the requirements, and point to the two ends of the hole center hole; to ensure the dimensional tolerance and shape and position tolerance of the bearing seat.
4、 Bench-work:Each thread bottom hole positioning hole to requirements of the bearing seat of the working roll.
5、 Bench-work:Other oil hole and screw hole drilling tapping;Clean and remove sharp edges of burrs for inspection. (first piece bearin seat for inspection)
6、 Final inspection: remove sharp edges of burrs by cleaning and send for inspection, and issue inspection list for the bearing seat.
Inspection and testing specifications for the bearing seat of the working roll on the transmission side of the hot rolling mill
material inspection
Composition analysis: ICP spectrometer (element deviation ≤± 0.01%)
Non destructive testing:
Ultrasonic testing (EN 12680-3 Class 1)
Magnetic particle inspection (ASTM E709, crack detection ≤ 0.1mm)
performance testing
Test project standard method qualification indicators
Static load test ISO 19973-1 1.8 times rated load without deformation
Dynamic fatigue test DIN 50100 10 ⁷ cycles without cracks
Sealing performance test ISO 5208 Class A 0.6MPa pressure holding without leakage
dynamic detection
Dynamic balance level: G0.4 level (ISO 1940-1)
Vibration intensity: ≤ 2.5mm/s(GB/T 29531)
FAQ
1. Can You Make This Bearing Seat for The Working Roll Product According To The Customer's Requirement?
A: Yes, we can follow your specific requirements.
2. Can I Visit Your Factory Before We Ordering ?
A: Yes, welcome to our factory for field trip.
3. Where Is The Nearest Port To You Company?
A: Shanghai port is the nearest one.
4. Can We Choose Different Materials for the bearing seat for the working roll ?
A: Yes, it can be selected depend on your requirements.
5. How Long will It Take And Deliver To Me For the Bearing Seat for The Work Roll?
A: It usually takes one and a half to two months by sea. It depends on the quantity of your order.
6. What Is Your Cover Of The Package?
A: We use wooden box to export.